Robotic Laser Welding vs. Manual Welding: Advancing Precision and Efficiency
- Henry Banks
- Sep 7, 2023
- 2 min read
Introduction:
In the world of manufacturing and fabrication, welding is a fundamental process that joins materials to create durable and functional structures. As industries evolve, so do the techniques used in welding. Robotic laser welding and manual welding are two distinct methods that have gained prominence. Both methods have their own set of advantages and applications, contributing to the versatility and efficiency of modern welding practices.
Robotic Laser Welding: Precision in Automation
Advanced robotics and laser technologies are combined in robotic laser welding. This method provides unmatched accuracy, reliability, and speed. This method involves programming robots with laser welding systems to follow predetermined trajectories, precisely delivering the laser beam to the welding site. This degree of automation ensures uniform weld quality and lowers the possibility of human error.
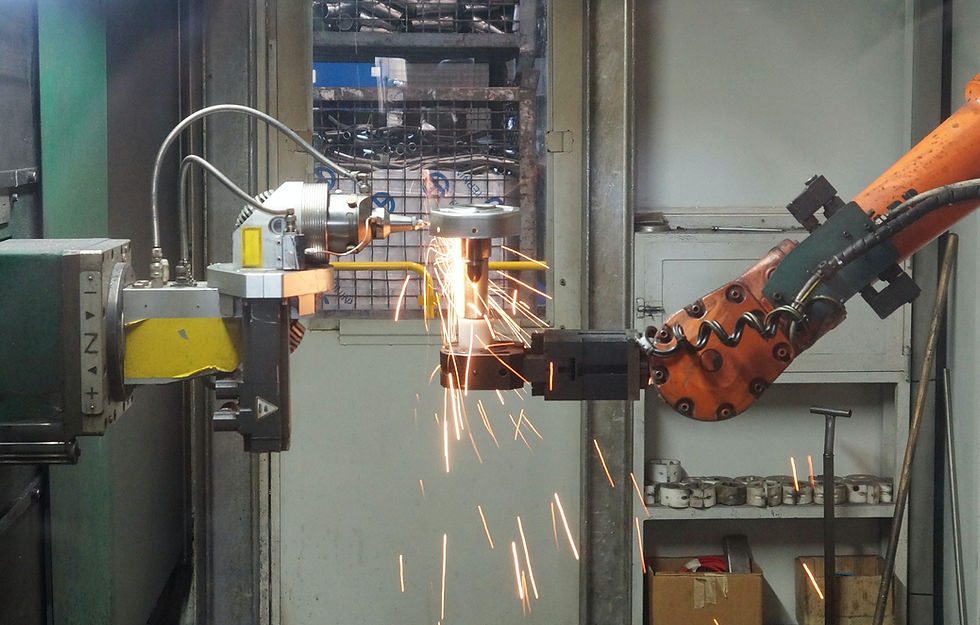
Robotic laser welding has a number of advantages, including its capacity to operate in intricate, cramped areas and carry out repetitive jobs without getting tired. Because of this, it is especially well suited for high-volume production in sectors like electronics, aerospace, and the automotive. Additionally, the laser's concentrated energy produces few heat-affected zones, lowering distortion and raising weld quality overall.
Manual Welding: Skill and Adaptability
Manual welding, on the other hand, relies on the expertise and experience of skilled welders. This traditional method involves using handheld welding equipment to join materials. While manual welding may not match the precision and speed of robotic laser welding, it offers a level of adaptability that is vital for intricate or custom projects.
Skilled manual welders possess the ability to adjust their techniques based on the material properties, thickness, and other factors, ensuring optimal weld strength and quality. Manual welding remains an essential process in industries that require a high degree of craftsmanship, artistic design, and quick adjustments.
Choosing the Right Technique for the Task
The decision to use robotic laser welding or manual welding depends on the specific requirements of the project. Large-scale production lines with consistent designs benefit from the speed and precision of robotic laser welding. This method reduces labor costs and maintains uniformity in weld quality. On the other hand, projects that demand a human touch, intricate detailing, or adaptability might favor the skills of a manual welder.
Harmonizing Efficiency and Craftsmanship
In the ever-evolving landscape of manufacturing, both robotic laser welding and manual welding hold their rightful places. Robotic laser welding excels in achieving high-quality, uniform welds in mass production scenarios, contributing to efficiency and cost-effectiveness. Manual welding preserves the artistry and adaptability of the human touch, making it indispensable for projects that require customization and finesse.
Conclusion:
The choice between robotic laser welding and manual welding is not about pitting one against the other, but rather about understanding their strengths and applying them judiciously. As technology advances and industries evolve, these welding techniques will continue to work in tandem to meet the diverse demands of modern manufacturing, ensuring precision, quality, and innovation in welding practices.
Comments